|
能源管理及余热利用控制系统的工作原理
该系统依托德国西门子公司先进的控制技术及控制系统,以精确的能源计量诊断技术为基础,对全厂的厂中的用能设备进行整合。制定出高效节能低排放的能源管理及利用方案并实施。
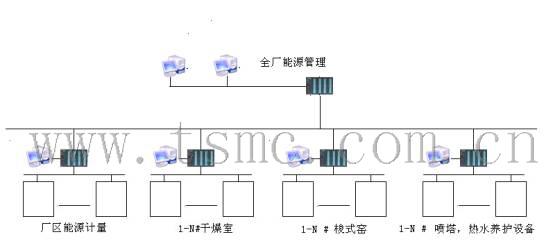
图2. 能源管理及利用控制系统的原理框图
工厂窑炉余热热源的分析计算
窑炉耗能
工厂的窑炉是5座以天然气为燃料的间歇式抽屉窑,单座窑炉一个烧成周期的设计燃料消耗量约为11,000 m3
余热热源
对现有同类型的窑炉热工记录进行分析,由烟气排出的热量(含制品冷却阶段的排热)为燃料产热的63%。
每座窑炉可稳定供热的时间为42个小时,(烟道温度高于300℃,排烟流量大于11,000 .Nm3/h),为整个含出/装窑时间的烧成周期的1/3左右。当窑炉的利用率为85%时,窑炉可稳定供热的周期重叠率为1.3,既可按单炉1.3倍的功率连续供热。
干燥房余热利用
干燥房能耗计算
新厂房内设计了干燥房10间,折合成150m3的标准烘房15间,每间干燥房的加热能耗为92,000 KJ/h, 干燥能耗56,000 KJ/h,
按加热/干燥房时间比例1:6计算,每间标准烘房的能耗为72,000 KJ/h(换算为85℃的热风,流量1470 m3/h)。烘房总能耗1,080,000 KJ/h。
使用余热热源的计算
主要利用窑炉冷却阶段排放的热能向烘房供热,不够时可调用中保阶段的排放(可按控制预案自动选择)。每座窑炉冷却阶段中可稳定供热的时间为20个小时,(烟道温度高于120℃,流量大于20,000 m3/h)为整个烧成周期的1/4左右。设干燥房的利用率为90%,如果五座窑炉正常生产,即可满足烘房对热源的需求。
节能减排经济效益分析
烘房利用率按90%计算,全年总体耗能8,398,000,000 KJ。
核减余热利用系统的电能消耗后,全年节能 7980,100,000 KJ 。折合天然气211,600 m3,.减少二氧化碳排放量约1800吨。
养护水池及厂房地热采暖余热利用
节能减排经济效益分析
热管式换热器效率按30%计算,全年总体换能:
3.8X106KJ / h * 2.1 * 24 * 365 * 30%=2.1X1010 KJ
每小时可提供大约2吨的80℃热水.
如使用2吨热水锅炉,小时耗煤量为0.28T,全年耗煤2500吨。二氧化碳排放量约6,350吨。
窑炉助燃空气预热余热利用
采用安装在烟道中的助燃空气换热器将助燃空气进行预热后送入窑炉燃烧器,可达到节能效果.每座窑炉升温过程可供换热的时间为38个小时,当助燃空气温度高于125℃,平均节能360,000KJ/ h.
节能减排经济效益分析
全年总体节能:
360,000 KJ/ h * 38 * 4 * 5 * 12=3.28X109 KJ
车间采暖余热利用
将冷却阶段的清洁热空气,输送到成型车间暖风系统,用于车间采暖.
经控制系统调配后,到达暖风系统的温度为35-40℃,流量30,000.S.m3/h.,当窑炉的利用率为85%时,既可连续供热。
节能减排经济效益分析
厂房采暖热负荷系数取160W/ m2,余热可满足5000 m2厂房的采暖需要.
核减采暖风机的电能消耗后,全年采暖节能 3.9X109KJ
折合天然气100,000 m3,减少二氧化碳排放量约1800吨。
余热利用项目经济效益分析
项目名称 |
干燥房 |
热水养护/采暖 |
空气预热 |
热风采暖 |
喷塔配风 |
节能
(KJ/年) |
7.89X109 |
1.4X1010 KJ |
3.28X109 |
3.9X109 |
1.7X1010 |
折合天然气
(m3) |
2.1X105 |
3.85 X105 |
8.9 X104 |
1.0X105 |
4.65105 |
节约费用
(万元) |
59 |
108 |
25 |
29 |
130 |
项目投入
(万元) |
128 |
96 |
已计入建窑成本 |
30 |
110 |
回收期
(年) |
2 |
0.9 |
|
1 |
0.8 |
能源管理及利用控制系统的整体经济效益:
由于贯彻了”优质优用,梯级利用”的能源利用方案,该系统的节能经济效益显著.
A.节能: 节约天然气 1.046 X106(m3) /年,按现行价格计算为350万元/年
B.减排: 每年减少二氧化碳排放量约一万四千吨
减去初期投资及系统的运行费用,运行五年的效益为:1200万元,减二氧化碳排放七万吨.
返回 |